Thermo Vacuum System
1. GENERAL INFORMATION
TVS – Thermo Vacuum System® in a patented equipment designed for thermal wood modification. The transformation is based on the use of high temperatures in vacuum
atmosphere, with no chemical additives.
The characteristics of the final product are substantial, first of all the increase of durability according the norm UNI EN 350-2:1996: this norm indicates the procedures to determine and
classify the natural durability of each wooden specie.
Moreover, also the mechanical properties are modified (also characterized according to ISO standards), and the wood colour.
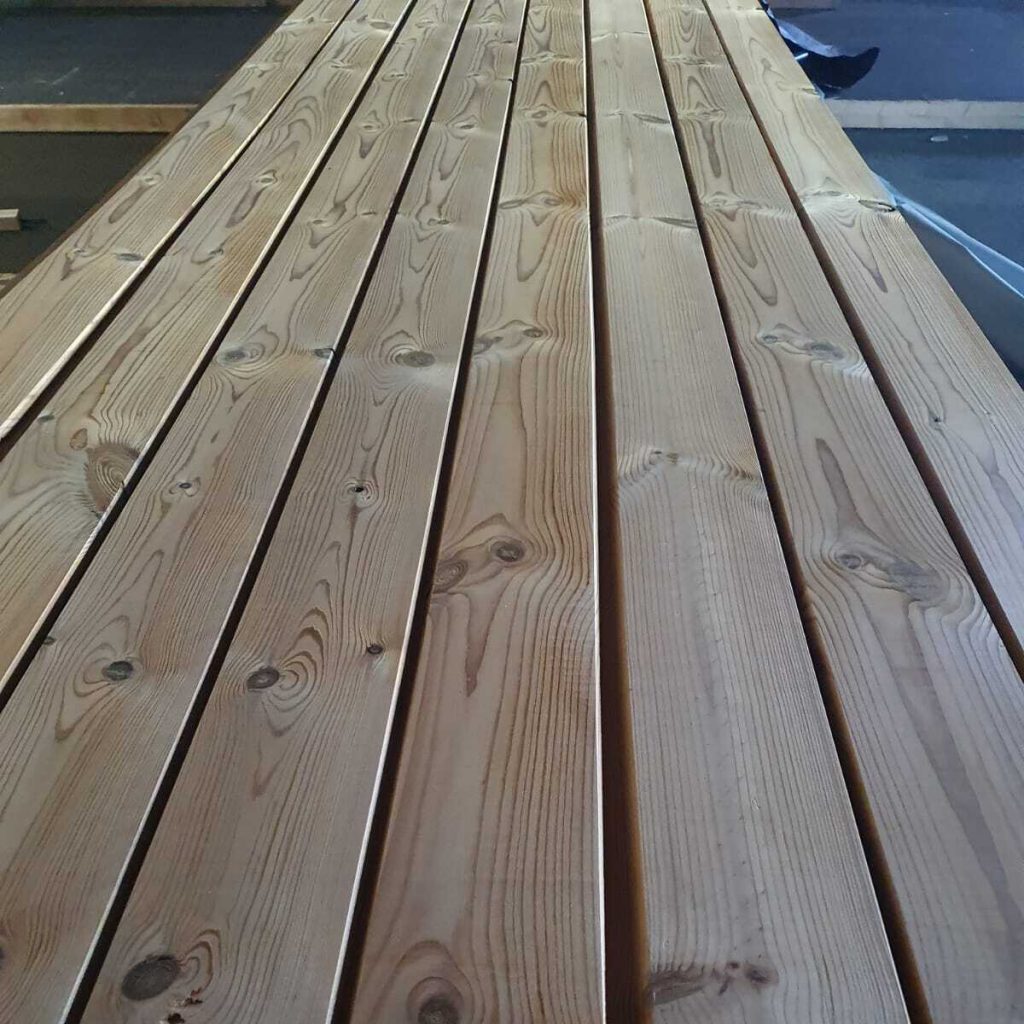
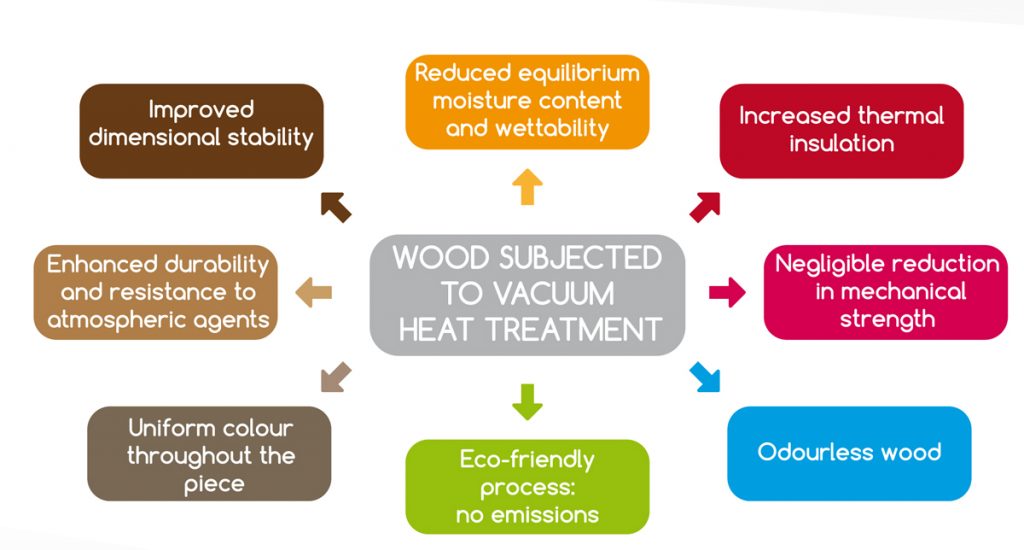
Finally, the Thermal Treatment Vacuum System advantages are many others, as described in the following picture:
- Reduced moisture content and wettability
- Improved dimensional stability
- Increased durability and weather resistance
- Uniform color throughout the product
- Environmentally friendly process
- Odorless wood
- Slight decrease in mechanical strength
- Increased thermal insulation
Heat-treated wood according to WDE Maspell research-based guidelines.
The TECH4WOOD project is recognized by the commercial name and the VacWood® trademark due to the characteristics and strength class. In addition, TVS heat-treated wood retains the evaluation criteria of the CEN/TS 15679 standard, which just defines the heat-treated wood characteristics.
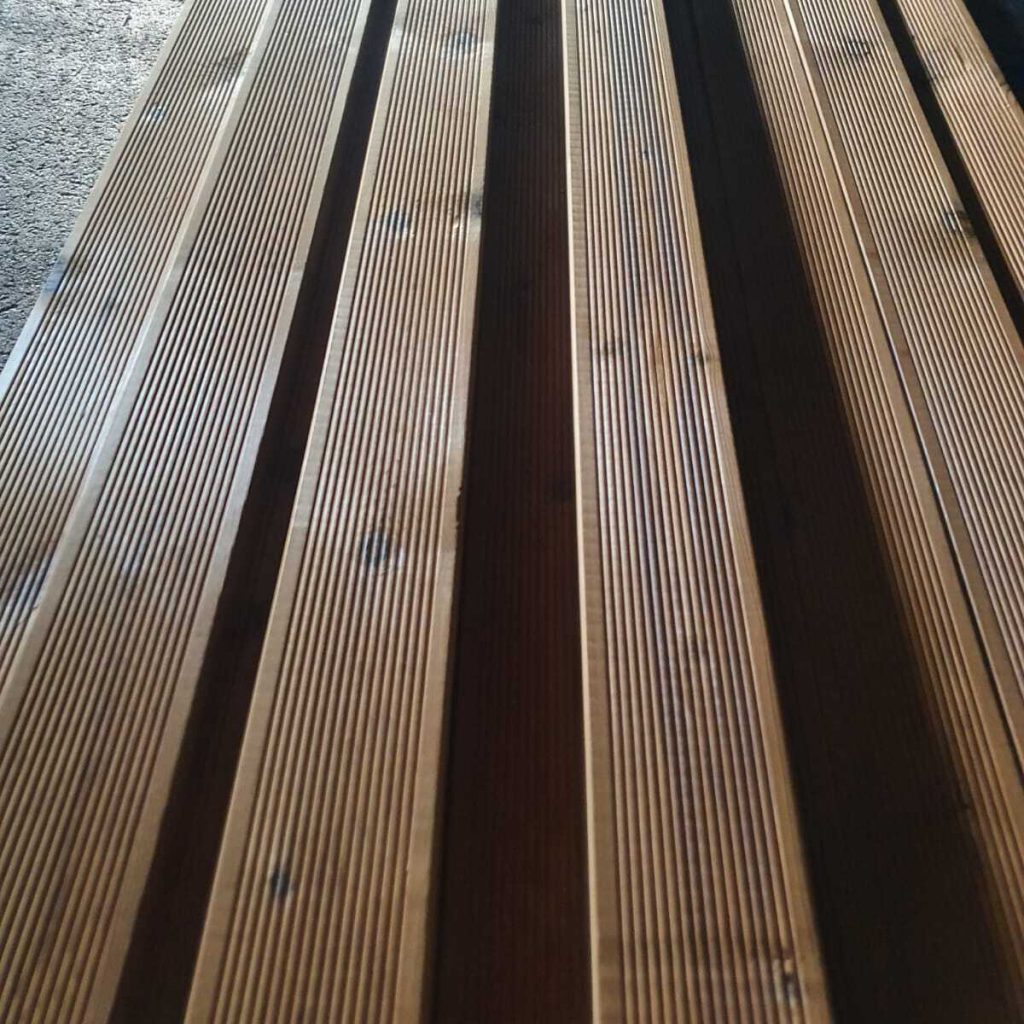
2. TIMING AND ENERGETIC PERFORMANCES
TVS Thermo Vacuum System® is a double-purpose system, usable for both drying and thermotreatment. This feature, unique in the market, allows to use the cell and dispose the load with the maximum flexibility.
Performance in terms of timing depend on wood conditions (Humidity and thickness): the process quality (according to WDE standard) is referred to initial homogeneous wood conditions.
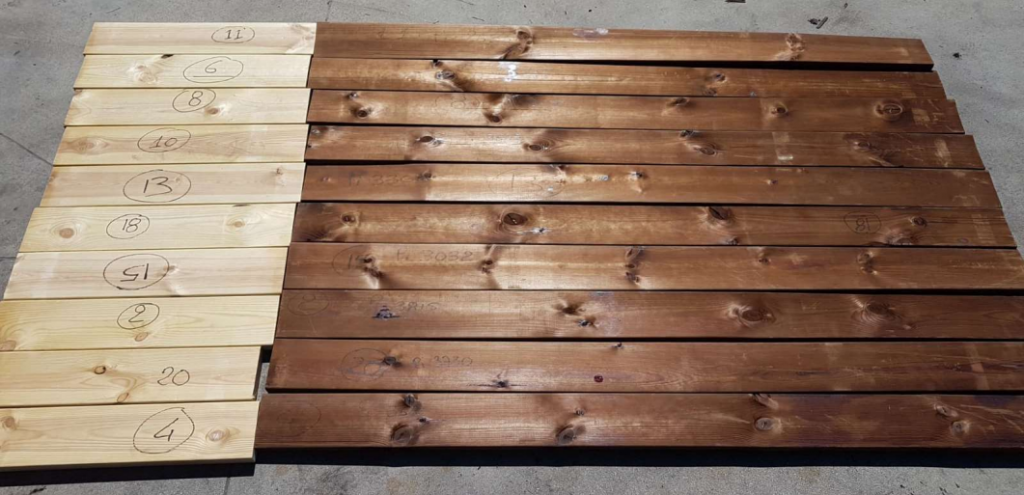
THERMOVACUUM TREATED WOOD
In case of a combined cycle (drying/thermo-treatment), economic saving varies between 9% and 30%, according to the type of wood and the initial conditions at the beginning of the cycle. Times and values of each cycle can vary in a range that assures anyway the final characteristics of the product both according to WDE standard and the norms; however, the Customer can modify the cycle parameters (inside the safety range) in order to personalize the production and the final results.
An adequate thermal insulation, as well as the correct and dot-like management of the heating system, based on the double control of the power and on the 4-spots measurement system, guarantee the maximum efficiency during heating and treatment temperature maintenance phase.
2.1 SPECIFIC PRODUCTION PERFORMANCE
Nominal productivity is calculated with reference to standard 60mm thickness; however, the actual simulation is made by keeping in consideration thicknesses and wood types as indicated by the Customer.
Drying cycle and process final results are showed and evaluated according to EN 14298:2018 norm, that defines evaluation criteria of the drying quality for saw timber.
Net actual production is calculated on the base of drying times so as obtained on the most commercial timbers worldwide, considering also loading and unloading operations; likewise, the net load per cycle is showed and calculated according to the Customer’s indications.
Stack dimensions are intended as complete with sticks, and measured at maximum footprint.
Stack dimensions: 1,2 х 1,2 х 13,5 м Number of trolleys 2
Here below, loading capacity and estimated cycle performances
WOOD SPECIE | PINE | SPRUCE | ASPEN | |
THICKNESS * | мм | 50 | 50 | 30 |
INITIAL MOISTURE CONTENT | % | 12 | 12 | 12 |
CYCLE NET LOAD 2 | M3/цикл | 30 | 30 | 26 |
PRE-HEATING GRADIENT ** | °С/ч | 10 | 10 | 8 |
FINAL CYCLE TEMPERATURE | °С | 210 | 210 | 190 |
ESTIMATED CYCLE TIME 3 | часов | 34 | 31 | 35 |
MONTHLY PRODUCTION | M3/месяц | 588 | 685 | 520 |
YEARLY PRODUCTION | M3/год | 6468 | 7535 | 5720 |
THERMAL CONSUMPTION 3 | КвЧ/М3 | 201 | 164 | 131 |
ELECTRICAL CONSUMPTION 3 | КвЧ/М3 | 43 | 38 | 43 |
1 Productivity is calculated on 330 working days, including the estimated ordinary maintenance time
2 Calculated considering 10% load loss and standard sticks, according to the thicknesses to be dried
3 Time and consumption estimation is referred to complete cycle (Preheating – Drying – Cooling) in standard temperature/pressure conditions.
* 50 mm and 60 mm can be single layer or double (25×2 or 30×2)
** Pre-heating gradient of 10° C/h is subject to the IMC 12% or lower.
Note: this is a technical proposal formulated according to customer needs and requirements.
3. CONTROL SYSTEM
Treatment process and all the system parts are controlled by PLC through an ultimate touchscreen panel; the TOTAL VISION® system allows the operator the remote management and control, through server connected to the Internet (from PC or Smartphone).
The control system allows to access the cycle parameters, to visualize the operation parameters of the auxiliary equipment, and to monitor consumptions and condensate quantity produced by the treatment process.
Moreover, the system grants access and can interact with information regarding the cycle timing as well as with the preliminary and final operations of ordinary maintenance.
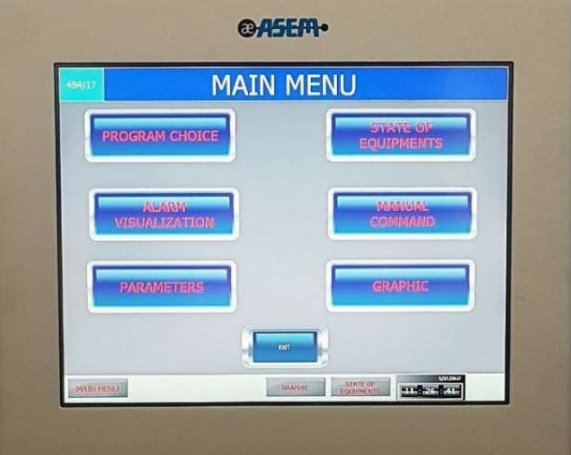
4. LOADING SYSTEM
The loading system is composed by stainless-steel external trolley and rails to allow the IN/OUT operations.
The rails can be drowned or at ground level, according to customer’s needs; this option will have to be specified before the preliminary approval of the layout.
Trolley handling can be made by fork-lift, by a pulley system or by a steel rigid rod. For larger dimensions models is recommended the use of power-driven mechanical handling of the trolley.
5. STACK TYPE AND STRUCTURE
The equipment design allows a wide range of stack dimension and length options, thanks to a stainless-steel flap, mounted on both sides of the trolley.
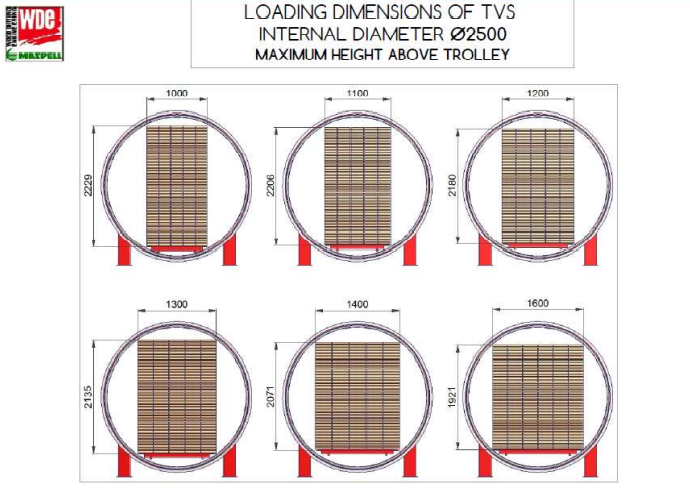
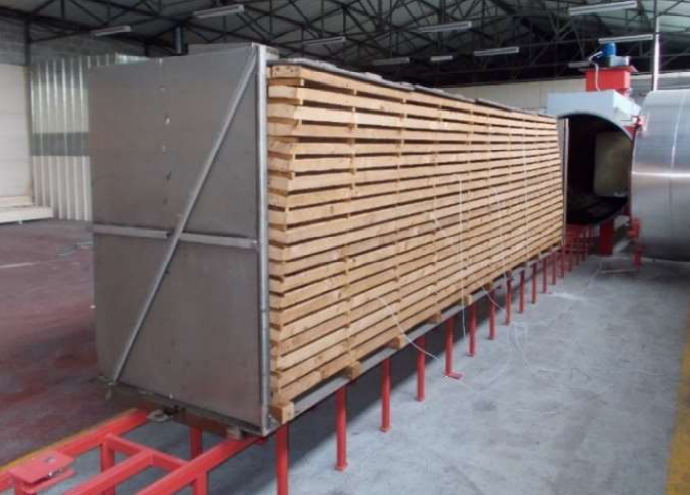
6. COMPONENTS AND CONSTRUCTION
The equipment has been designed to withstand the atmosphere and temperature variations of the TVS process. All the parts of the cell in contact with the treatment environment, as well as hoses, are built in stainless-steel AISI 304.
Also fixing of the parts exposed to the treatment is in stainless-steel, while other parts are in mild steel. Components are assembled and tested either at the arrival in our plant and during the start-up phase at customer’s site. Inverter technology engines are mounted for the maximum efficiency.
Thermal insulation is composed by high density rockwool, and the external coating that protects the insulation is made by aluminium, to guarantee a very long duration.
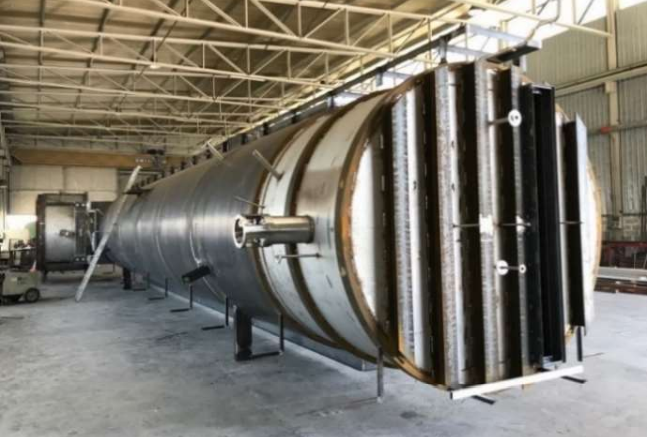
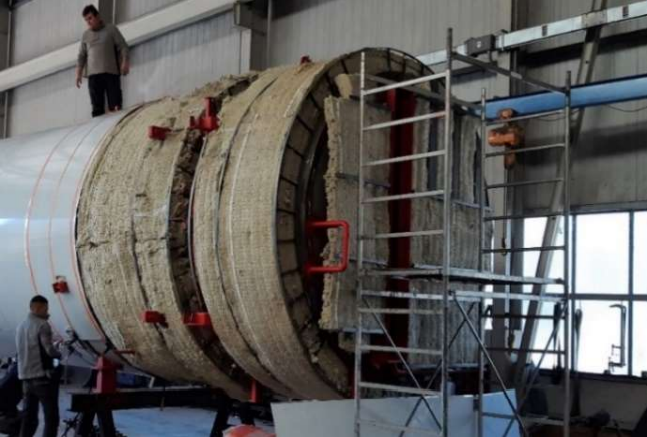
7. PRIMARY AUXILIARY SYSTEMS
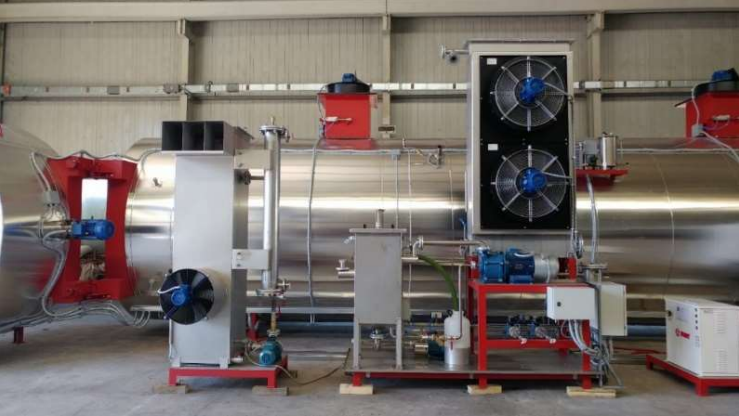
For the proper operating of the TVS system, it is provided with a wide range of auxiliary equipment for the fluids management during the different of the cycle.
All auxiliary equipment are built in stainless-steel grade AISI 304 and 316, included condensers, pumps, and valves for the management of steams and condensate fluids.
Major auxiliary systems include:
- HEATING SYSTEM
- CONDENSER
- COOLING TOWER
- CELL COOLING SYSTEM
- INTRINSIC SAFETY SYSTEM
- 24V SAFETY SUPPLY SYSTEM
- TELEPHONE DIALER
- INERTIZATION IN HYDROGEN
- AUTOMATIC WASHING SYSTEM